
Design for simplicity,
Design for success.
The Challenge.
The 2018 RobotX competition in Hawaii challenged the team to collect six rings placed at various depths underwater.
The main objective was to develop an autonomous underwater ring retrieval system which eploys minimal computational power, pre-existing surface maneuvers, and an in-vessel control to complete the challenge
Given the team’s software/electrical/mechanical capabilities it was decided that the challenge is to be actuated from above the waterline
Developing a Solution.
To completely understand the task, limitations, requirements, and physical behavior of the challenge, I developed real-size competition spec. elements to simulate the environment, magnitude, and behavior of these elements. This allowed the us to successfully assess the efficacy of the design solutions in the testing phase.
Created drawings and sketches to quickly convey ideas and gather input from team members and professors about design features, improvements, and possible modes of failure
Assessed key design features to plan maneuvers and solutions with other sub-teams in order to develop ideas which are conscious of the team’s capabilities, time frame, and complexity of design
The Solution.
Although out-of-the-box, the solution ended up playing a pivotal role in the competition. While other teams dealt with the complexity of integrating two autonomous vehicles or using computer vision to detect individual rings under water. Our solution proved significantly less complex and ultimately very successful. Key characteristics include:
Variable depth hook location
Pivoting system and main axis
System of thrust bearings to prevent longitudinal motion of the shaft
High torque electric motor used to drive the rotational motion of the hooks underwater
High-torque water-tight OTS winch assembly used in system deployment
Design Features/ Manufacturing.
Pivoting and Rotating Hook System .
The design employs a series of sweeping/rotating hooks which capture the buoyant rings with a success rate of approximately 95%
In order to reduce drag, the rotating system was placed on a pivot above water where it rests horizontally until it is deployed
The hooks are rotated using an Enstort motor from above water since dynamic sealing is not within our mechanical capabilities
Several attachment methods were developed, prototyped, and tested to arrive at the design previously shown
Materials and Manufacturing.
Most of the system uses 6061 T6 Aluminum because of its machinability
Several processes were used in the manufacturing of the system
Manual mills, and lathes were employed in addition to welding and hot working Aluminum metal
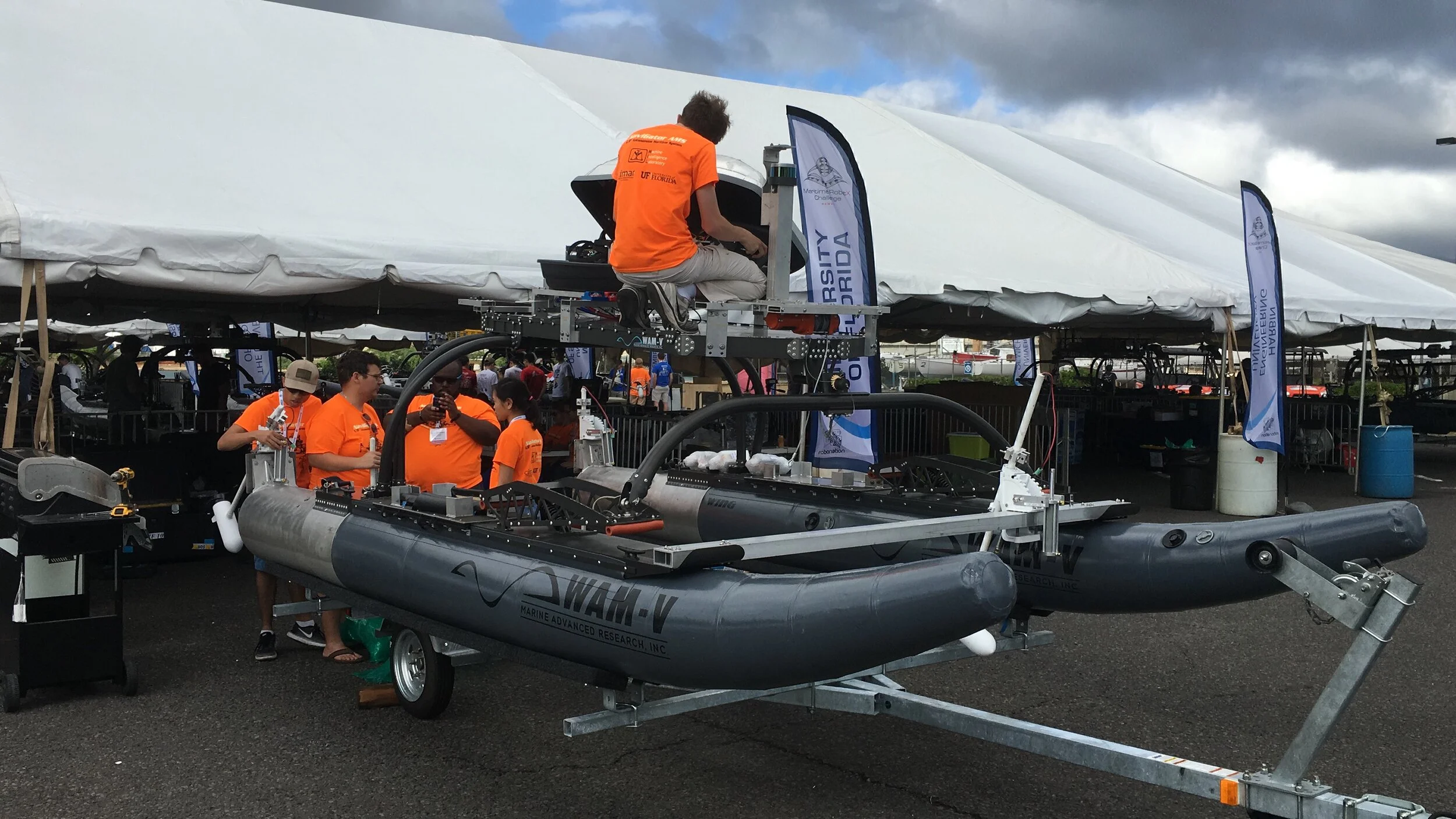
